Non-Switching Driver
The non-switching driver controls the rotation of an air spindle, which is a rotating mechanism typically found in disk test equipments. Because the equipments used to manufacture and test hard disks used in many personal computers and home appliances handle small signals, it is important to reduce the electromagnetic noise of non-switching drivers, while maintaining high-precision rotation speed.
We offer a non-switching driver that suppresses the noise caused by the non-switching (linear) operation of the power device that drives the motor, while achieving high-precision, high-speed rotation through PLL control* 2 by encoder signals*1.
- *1 Encoder signal: A rectangular clock signal according to the rotation speed output from the encoder mounted on the spindle to detect the rotation speed.
- *2 PLL control: A method of maintaining high speed accuracy by synchronizing the rotation reference clock commanded from the host device and the encoder pulse built into the air spindle.
NS20-A
Suitable for applications measuring small signals that detest ON/OFF noise
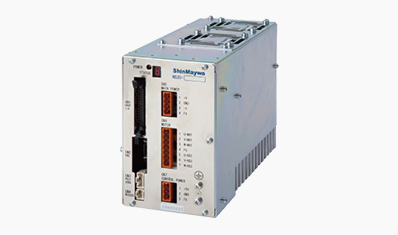
- Realizes environmental free of switching noise
- Equipped with non-switching (linear) type power element
- High response current control
-
Equipped with PLL control and torque (current) control mode.
The control cycle of the control loop is as short as 10μs, enabling highly accurate control.
Also compatible with CLV (constant linear velocity control).- *CLV (Constant Liner Velocity):
In disk inspection equipment such as HDDs and DVDs, rotation control that changes the rotational speed of the disk depending on the position of the head and maintains a constant speed at which the head traces the disk.
- *CLV (Constant Liner Velocity):
- Expansion of motor compatible range, expansion of encoder pulse compatible range
- The number of motor poles corresponds to all the number of poles (4 to 42 poles) of our BUILT-IN DD. The encoder can handle up to 1 million pulses per revolution. Additionally, signal frequencies up to 5MHz can be received.
- Compliant with European RoHs Directive
- Compliant with the European Union's directive "RoHS Directive" (directive on the restriction of the use of specific hazardous substances in electronic and electrical equipment).
Outside Dimensions
(Unit: mm)
This section shows the appearance and dimensions of the driver.
Figure 1 shows the external appearance and driver dimensions.
Figure 2 shows the M3 tap mating dimensions for installation.
Mass: approx. 3kg
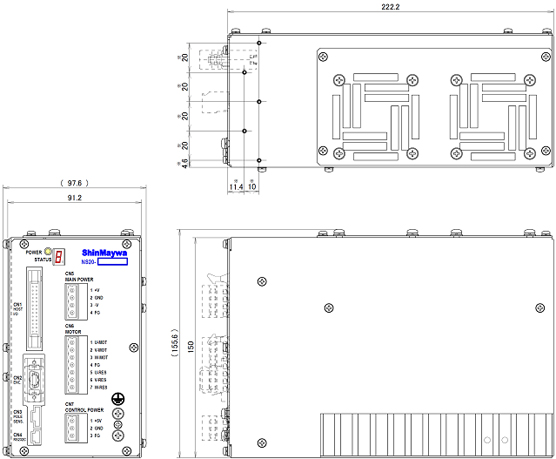
- * Dimensions marked are the same as the M3 tap connection dimensions of the old product (NS20-**)
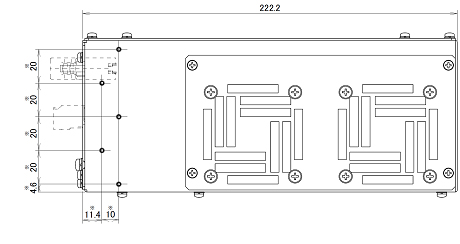
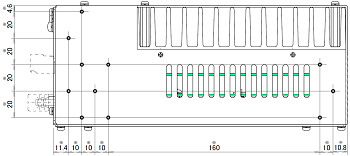
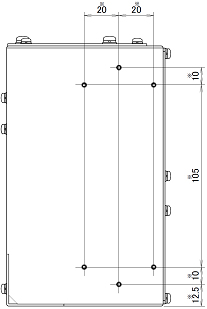
Figure 2 Installation dimensions
Length of M3 threaded bolts must be fixing plate thickness plus 5 - 6mm. If the bolt length is too long that may cause internal contact.
Main Specifications
Dimensions & Performances | Specifications | |
---|---|---|
Type | NS20-A | |
Applicable motor | Three-phase synchronous motor *1 | |
Applicable Encoder | Incremental encoder (maximum 5MHz) *1 | |
Power supply | Main power supply | ±24V (8.5A or more) |
Control power supply | +5V (1A or more) | |
Output Power | Maximum Output | 8A peak |
Continuous Output | 5Apeak (4.5Apeak at extremely low speed) *2 | |
Control Details | Output Stage Method | Non-switching (linear) operation inverter sinusoidal current control |
Control Mode |
|
|
Control Input | Rotation command, direction command, reset, etc. | |
Control Output | Encoder pulse (A, B, Z phase), PLL lock, motor stop, alarm, etc. | |
Uneven Rotation | 0.001% or less *4 | |
Anomaly Detection |
Displayed on 7segLED etc. |
|
Abnormal Braking | Dynamic brake (with built-in resistor) | |
Surrounding Envrionmental | Temperature: 0 to 40℃ (driver ambient temperature during operation) Humidity: 85% or less (no condensation) Do not install in an atmosphere harmful to electronic circuits. (corrosive gas, metal powder, moisture, oil, etc.) |
|
Storage Temperature | Temperature: -15 to 80℃ (driver ambient temperature) Humidity: 85% or less (no condensation) |
|
Cooling Method | Forced air cooling (built-in cooling fan) | |
Weight | 3kg |
- *1Application is to be judged for each product.
- *2 In the early stages of startup or when the product is almost at a standstill, the current limit value will automatically switch from 8Apeak to 4.5Apeak.
The rotation speed derived from the following calculation formula is shown below.
(4[Hz]/(number of poles/2))×60[r/min] - *3Used when dividing precision of encoder pulse is insufficient.
- *4It could be 0.001% depending on load or rotation speed.
Contact Information
Click here for product inquiries.
Search for other products and services