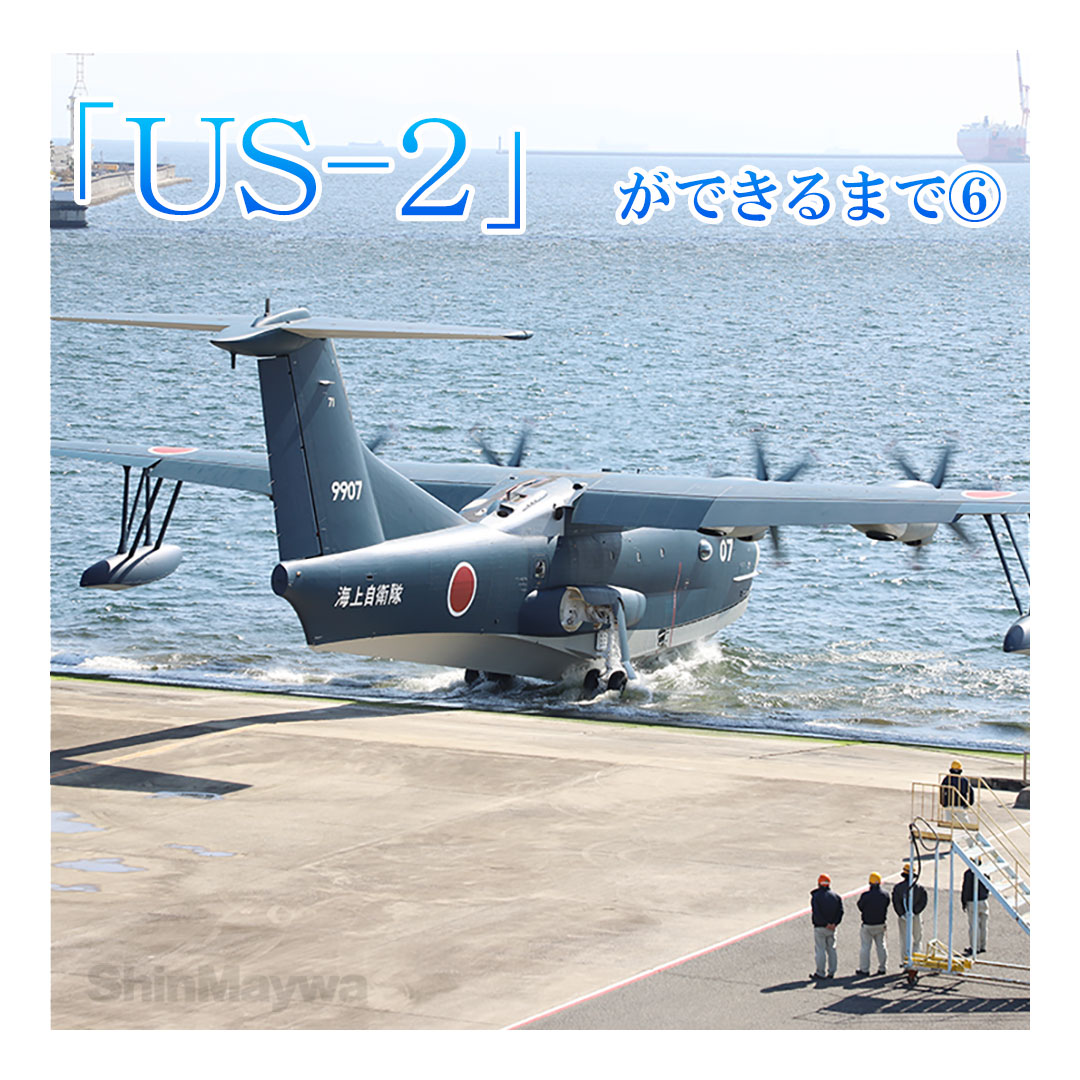
-プロのライターが密着取材!
機体組立
「ブロック工法」で、効率的につくっていきます
前回に引き続き、「US-2」の機体組立の工程をご紹介します。
前回は、パーツを組み合わせてフレーム(円框(えんきょう))とストリンガー(補強材)で骨組みをつくり、そこにスキン(外板)を張っていくという「セミ・モノコック」構造のお話でした。「US-2」のような大型機の場合は、これを複数のブロックにわけて並行してつくり、それらを最後に組み合わせて一気に航空機の形に仕上げていきます。これを「ブロック工法」といいます。
ブロック工法により、作業を大幅に効率化できます。
たとえばスキンをリベットで留める際、裏側から支えが必要になる場面がありますが、ブロック工法なら簡単に裏側に作業員が回り込めますし、意思疎通や合図もしやすくなります。
また、技術力のある協力会社(サプライヤー)の工場でも並行して作業できるというメリットもあります。実際、「前中胴(ぜんちゅうどう)」といった機体の大きな部分も協力会社が製造しています。機内搭載の電子機器等も含めると、「US-2」には約1,400社が参画しているそうです。
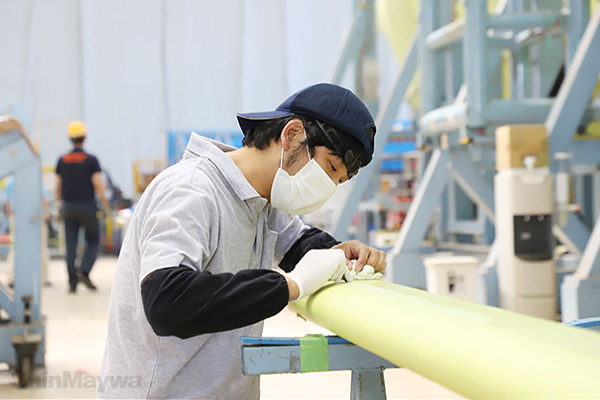
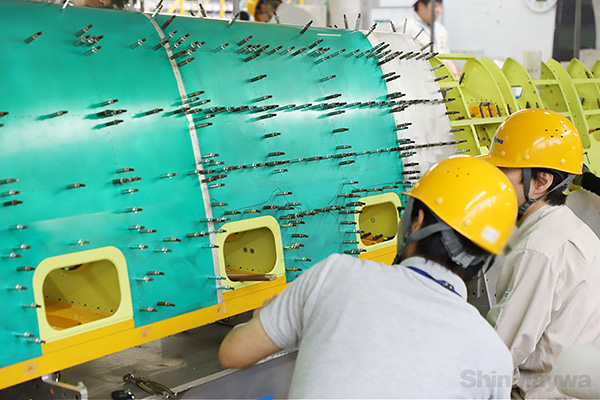
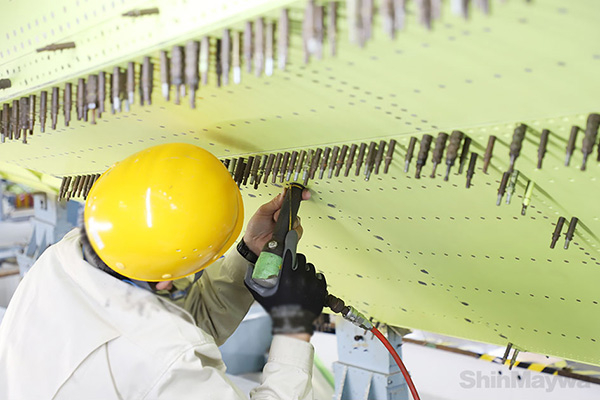
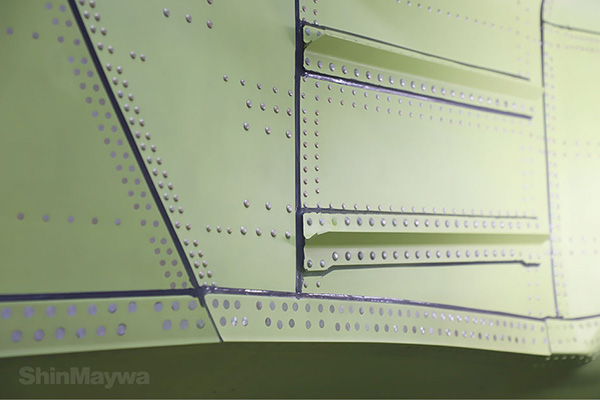
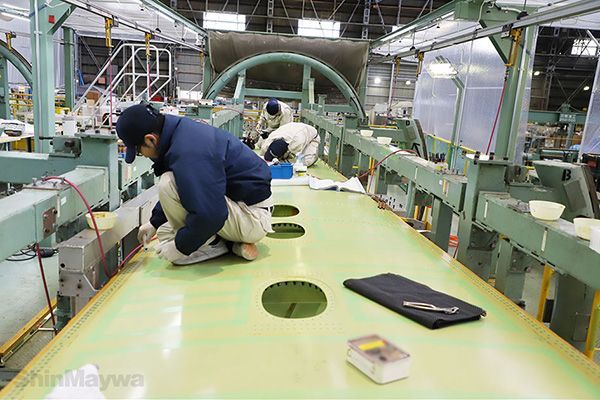
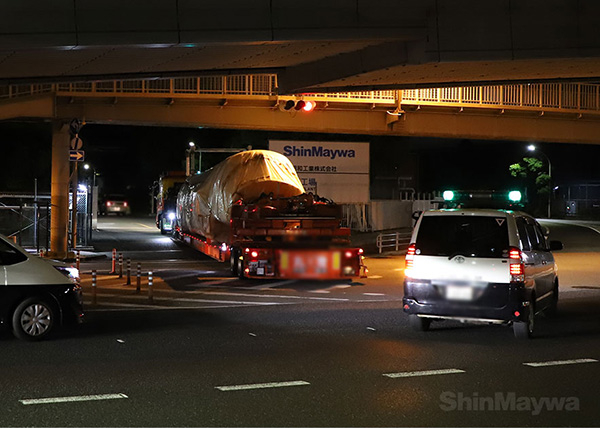
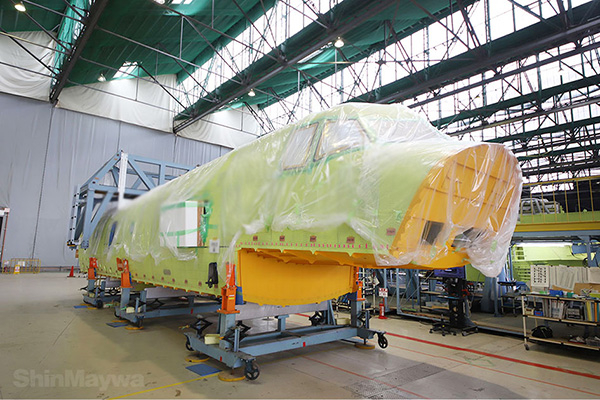
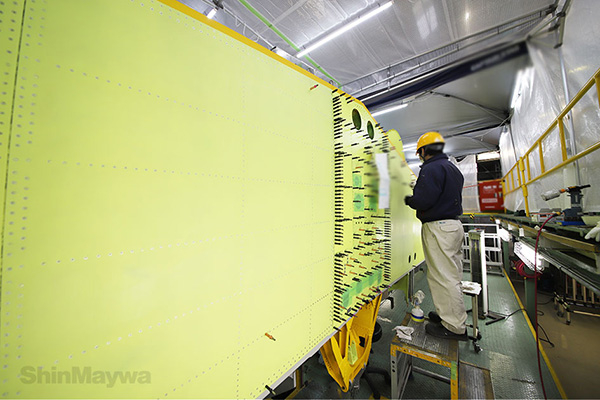
新明和工業は、川西航空機時代から飛行艇の設計・製造のノウハウを受け継いでいますが、その設計に従って多くの企業が自社の技術を発揮してつくっているわけです。“日本の技術力の結晶”ともいえるのかも知れませんね!
ライター 板倉秀典
- ※本連載は、防衛省の許可を得て制作、掲載しています。内容および画像の転載はご遠慮ください。
テーマから探す
#社会インフラを支えています
#サステナビリティ
#パーキングシステム
#輸送
#3つの領域
#環境
#都市
#新明和グループ
#流体
#AI
#アップサイクル
#保守
#研究開発
#川西航空機
#川西機械製作所
#新規事業
#水素
#採用
#産機システム
#特装車
#航空機
#機械式駐車設備
#US-2
#真空装置
#航空旅客搭乗橋
#自動電線処理機
#環境システム
#DDモータ
#民間航空機事業
#塵芥車
#テールゲートリフタ
#飛行艇
#ダンプトラック
#リサイクルセンター
#水中ミキサ
#アームロール®
#脱着ボデートラック
#ごみ中継施設
#水中ポンプ
#XU-L
#XU-M
#甲南工場
#XU-S
#製品紹介
#エレパーク®
#ループパーク®
#US-1A改
#パックスウェイ®
#佐野工場
#US-1
#PS-1
#UF-XS
#US-2ができるまで
#マンガ暮らしを支える新明和
#お知らせ
#真空成膜のお話
#歴史
#イベント