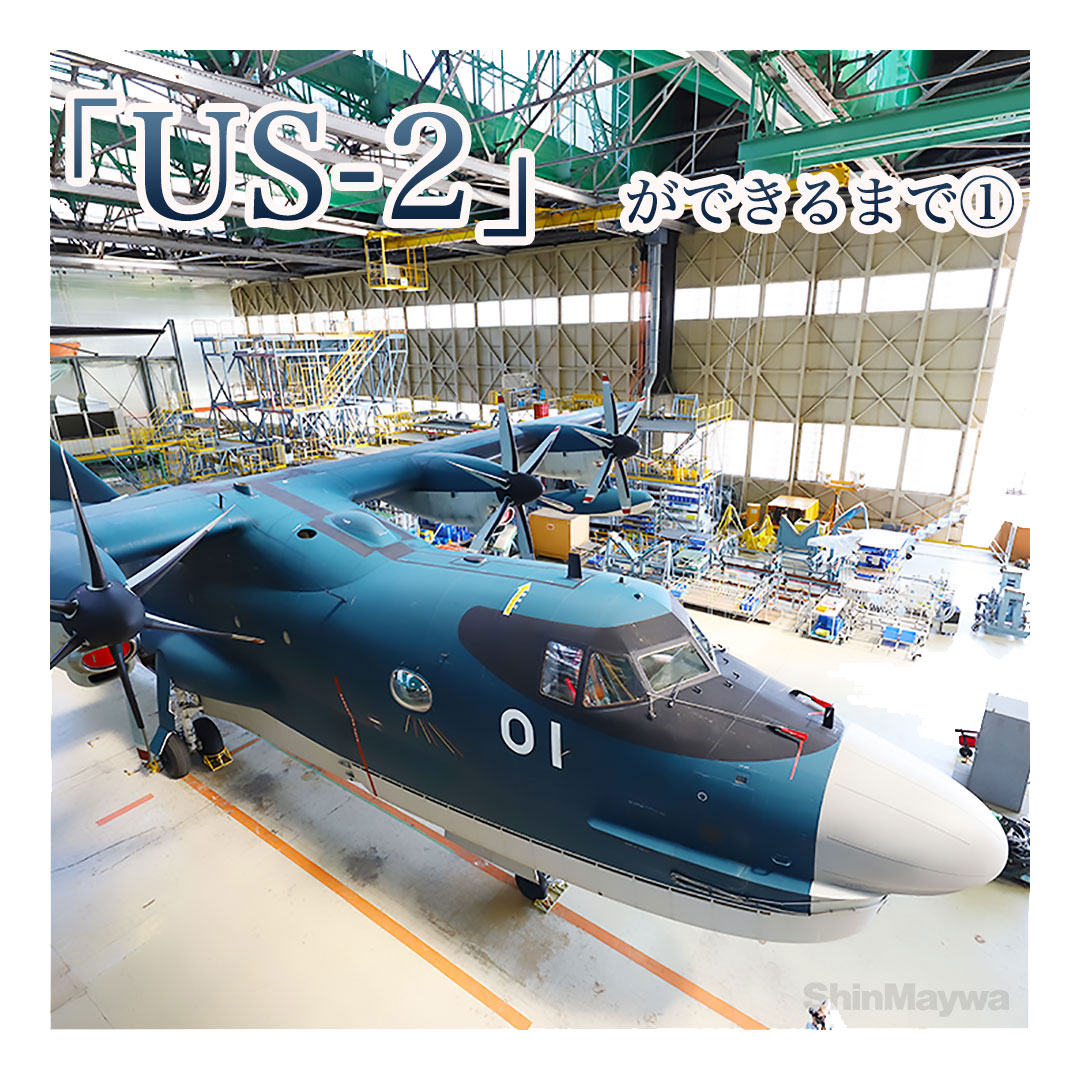
-プロのライターが密着取材!
部材の切り出し
「US-2」は、ほとんどアルミでできています
世界最高性能の飛行艇「US-2」の製造工程にプロのライターが密着。シリーズでお伝えします!✨
有名酒造会社の酒蔵が多く立ち並ぶことで知られる兵庫県神戸市東灘区。「US-2」を製造する新明和工業の甲南工場は、そんな街の一角にあります。
一般的に航空機の工場は、滑走路に隣り合った場所にありますが、飛行艇の場合は水面を離着水できますので滑走路は必要ありません。甲南工場も海に面していて、完成した飛行艇は神戸沖の海面で離着水します。近くに滑走路がないこともあって、地元の方でもここで航空機がつくられていることを知らない人も多いようです。
甲南工場では、防衛省との契約に従って「US-2」を製造しています。ここでは艇体と呼ばれる胴体部分や、主翼、尾翼など翼の大部分をつくり、海外を含むパートナー企業が製造した装備品などを運び込んで組み付けていきます。
今回は、そんな「US-2」製造の最初の工程をご紹介しましょう。
「US-2」の最初の姿は、アルミの板とブロック
航空機の多くは、軽さと丈夫さを両立するために機体の大半がアルミ合金でできています。「US-2」の場合は、必要な強度に応じて数種類のアルミ合金を使いわけるなど、材料が細かく指定されています。「US-2」製造の最初の工程は、素材メーカーでつくられたこれら種類のアルミ合金の板やブロックから、部品を切り出したり削り出したりする作業です。
アルミ合金の板からのパーツの切り出しは、NCルータという工作機械を使います。NCルータにデータを入力して、1枚の板から数点~数十点の“パーツの素”を切り出すことができます。このパーツの素は、次の工程で職人がほぼ手作業で穴を開けたり曲げたりしてパーツの形状に仕上げていきます。
こうしてつくられるパーツは、熱処理(次回で説明します)することで硬くできますが、もっと強度が必要な部品をつくる場合には、アルミ合金の薄い板からではなく、塊(ブロック)から削り出します。この作業には汎用フライス盤やNC旋盤という工作機械を使用して、こちらも一つずつ手作業でつくっていきます。
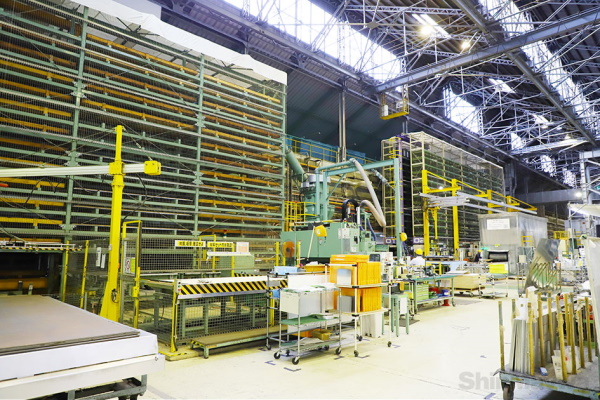
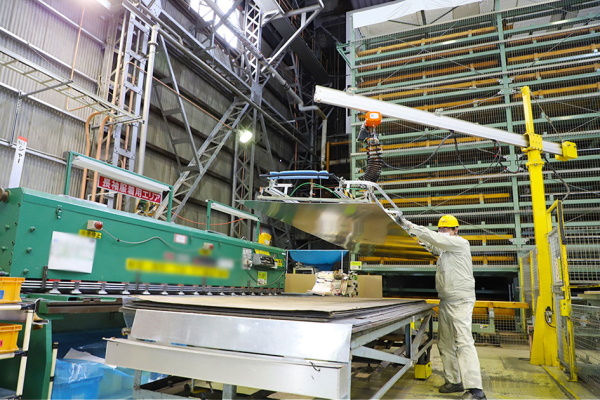
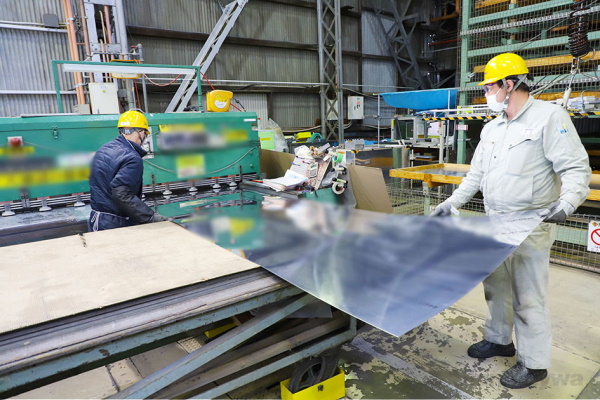
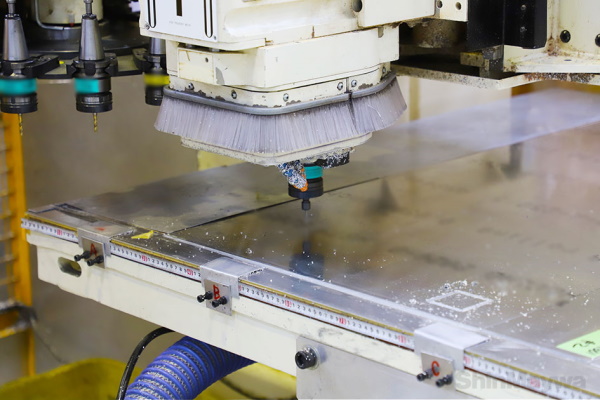
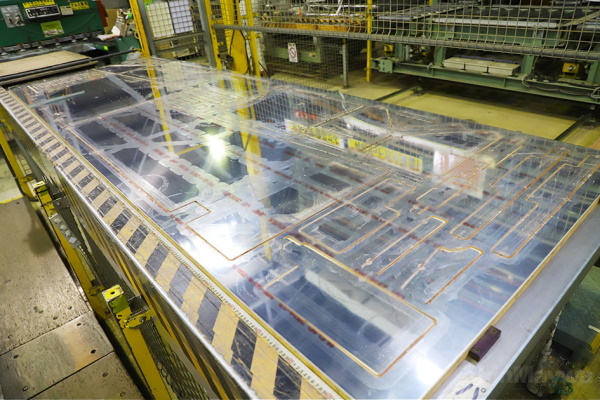
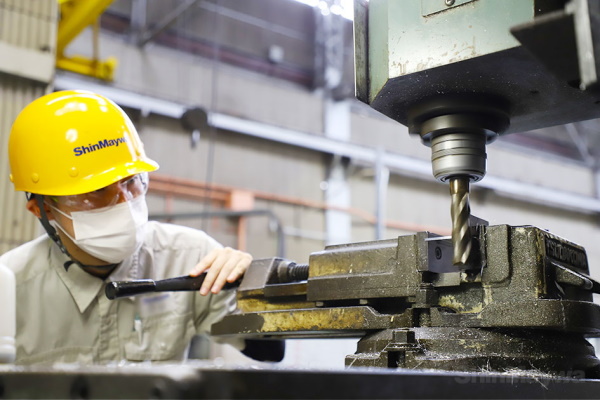
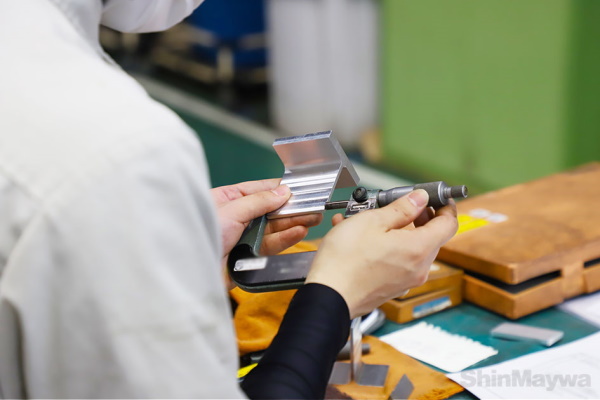
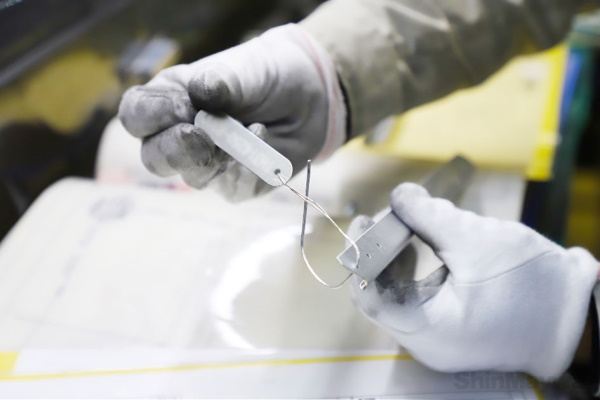
思ったより手作業が多くて驚いたという方もいるでしょう。しかし、これにはちゃんと理由があります。大半のパーツが数年に1個~数個しかつくられないため、パーツを自動で量産できる設備をたくさんそろえるよりも、熟練作業員による手作業のほうが、コストがかからず効率も良いのです。ちなみに、海外の巨大航空機メーカーでも製造過程の多くで手作業に頼っています。飛行機をつくるのって、大変なんですね。
ライター 板倉秀典
- ※本連載は、防衛省の許可を得て制作、掲載しています。内容および画像の転載はご遠慮ください。