[Series] How the US-2 is made (4)
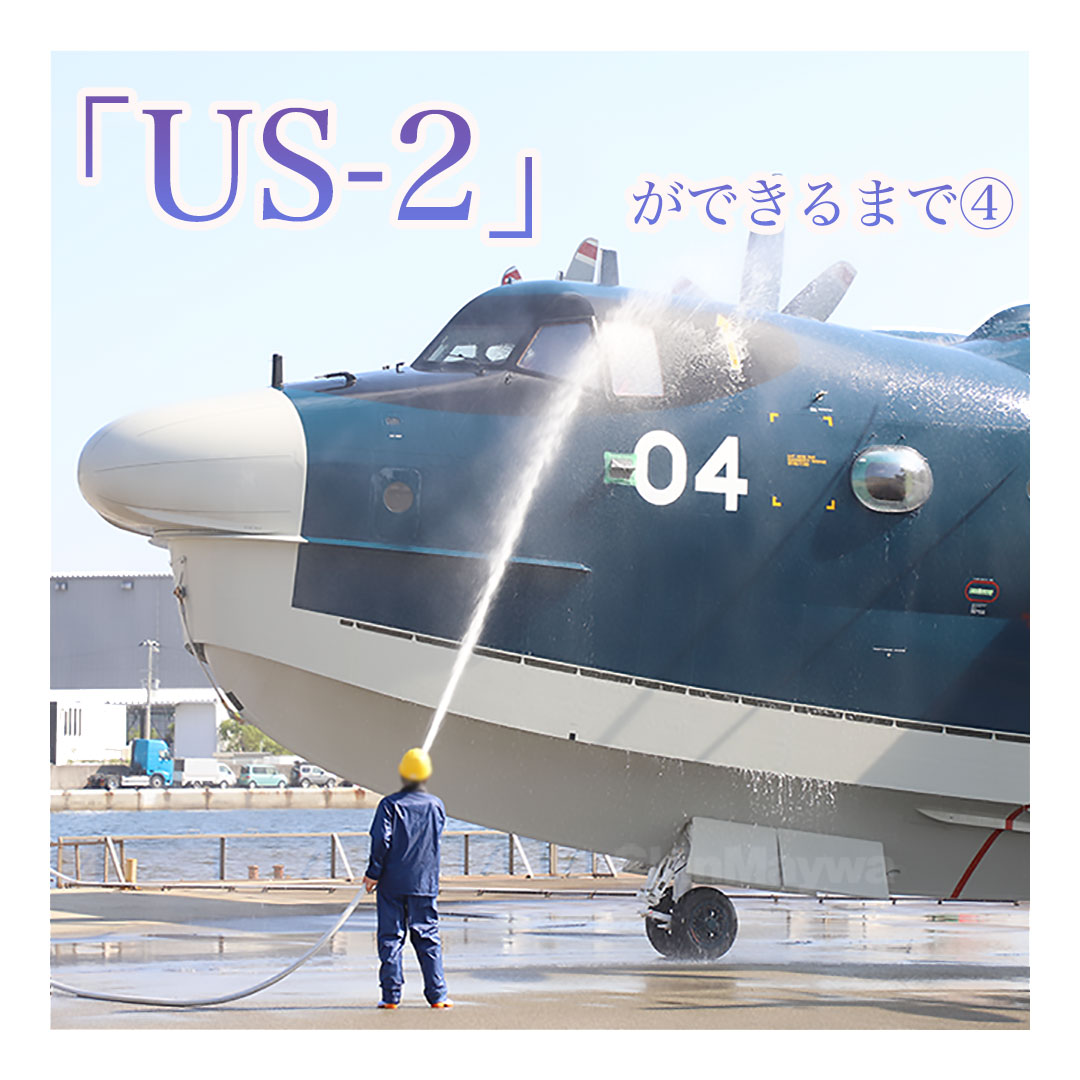
Close coverage by a professional writer
Coating of parts
—Skilled craftsmen's skills are evident in the coating process
The surface treatment process was introduced in Part 3. After surface treatment, parts of the US-2 are carried into the coating booth within the specified time and coating is applied. The primary purpose of this process is to increase the parts’ corrosion resistance. The coating film protects the part’s surfaces from exposing to seawater etc.
The first coating applied in the coating booth is called the primer. The parts of the US-2 are painted with yellow primer. Therefore, a yellow US-2 will appear when the parts are assembled in the following process. US-2 has the image of dark blue and this is the color of the coating called the topcoat, which is applied to the entire airframe after assembly.
The yellow primer is so to speak the base coat. The number of coatings, film thickness (coating thickness), and other application methods are specified for the airframe surface and the components inside the US-2. The thickness of the coating is as thin as a human hair.
If the coating is thinner than this, corrosion resistance will be decrease. Conversely, if it is thicker, the airframe will be heavier than planned. This is another example of the difficulty of manufacturing amphibian aircraft. It must be lightweight but must be resistant to be exposed to the seawater. Therefore, this coating process is also done by hand, without relying on machines.
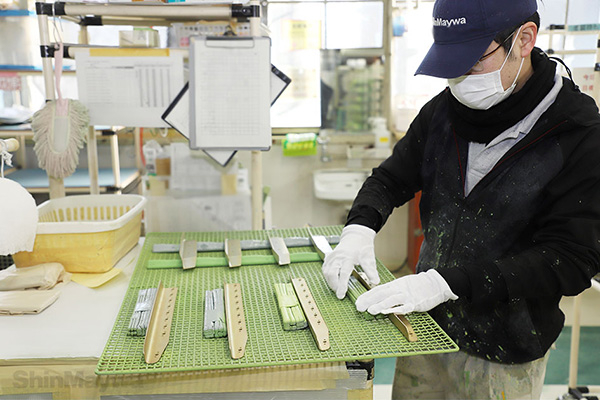
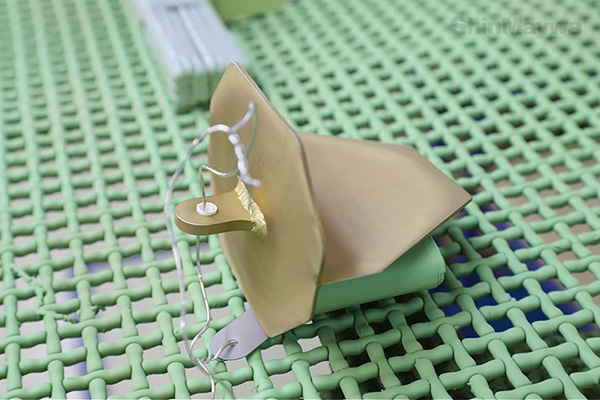

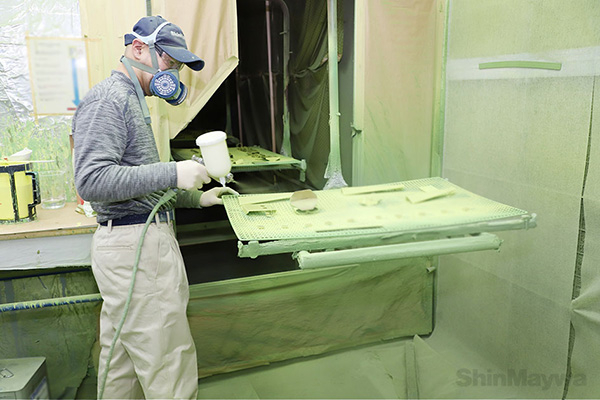
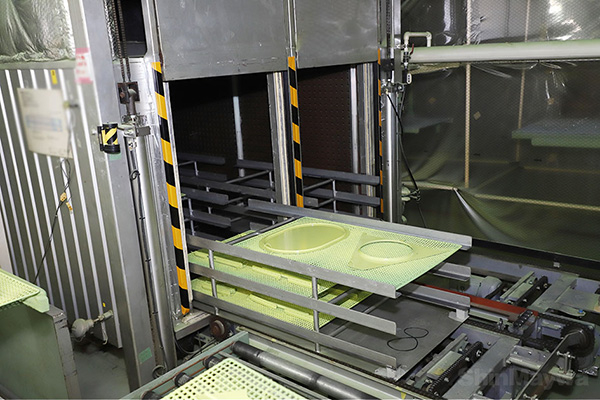
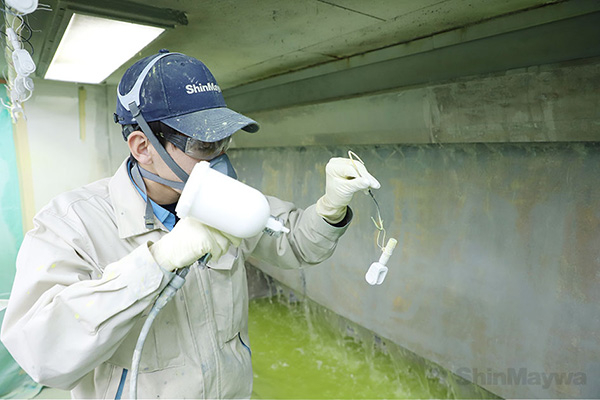
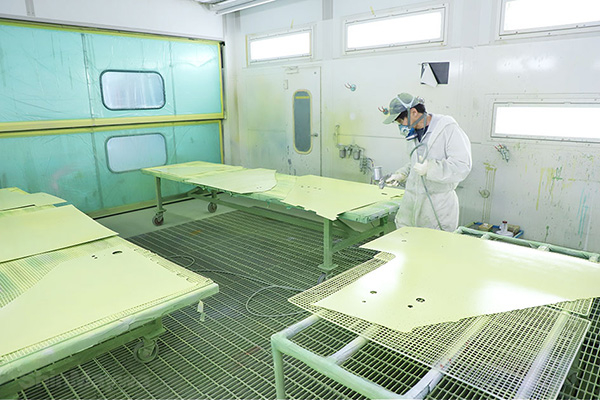
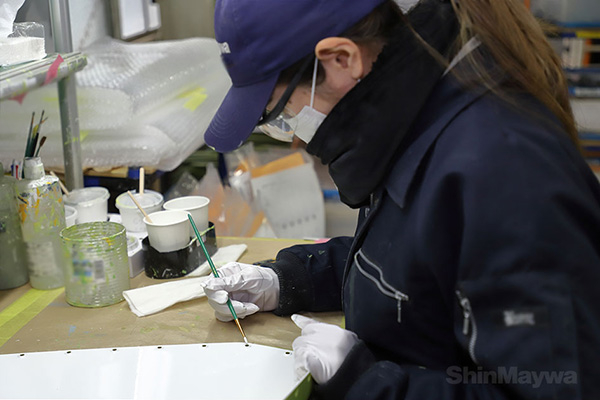
Writer Hidenori Itakura
- *This series is produced and published with the permission of the Ministry of Defense. Please do not reproduce the content and images of this series.