[Series] How the US-2 is made (3)
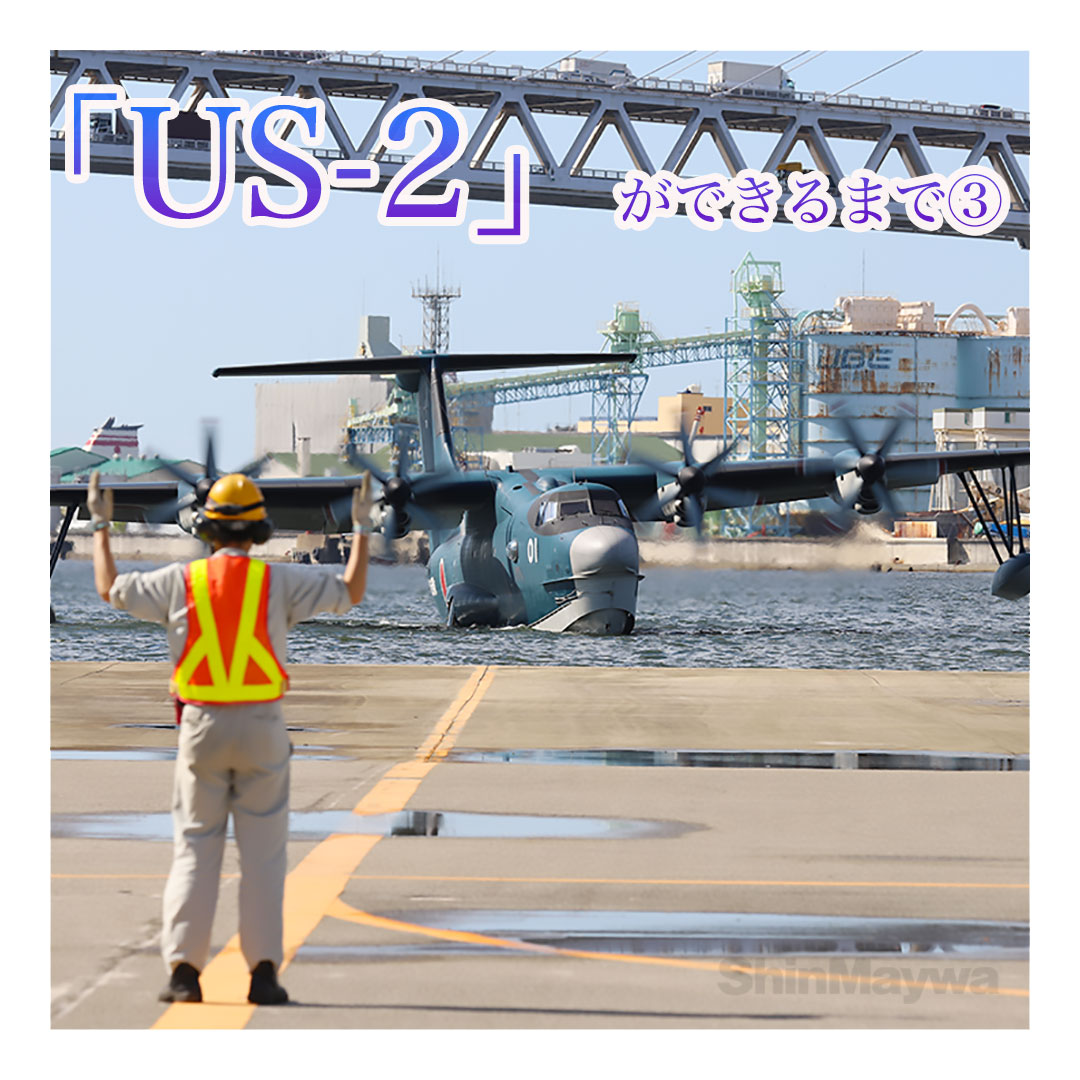
Close coverage by a professional writer
Surface treatment
—Making parts resistant to corrosion and strong against seawater
As described in the first issue of this series, the US-2 is mostly made of aluminum alloy. Aluminum is a relatively corrosion-resistant metal. However, seawater is still its natural enemy. Unlike other aircraft, the US-2 is routinely exposed to seawater. There is a "wash rack" facility at air bases of the Japan Maritime Self-Defense Force, where airframes are washed entirely to rinse salt off after each flight. This is one of the treatments to prevent corrosion.
Since the US-2 is operated under such harsh conditions, thorough measures against corrosion are taken from the time of manufacturing. That is to say, surface treatment and coating (the coating process will be introduced in the next issue).
As the name implies, surface treatment is a process which is applied to metal surface to change its properties. Its purposes vary: increasing wear resistance, creating a glossy and beautiful look, strengthening against heat, or scraping off part of the surface. For aluminum parts of the US-2, several surface treatment methods are performed mainly to improve corrosion resistance and to prevent the coating from peeling off. Konan Plant has a dedicated facility for surface treatment where most of the parts are processed.
Surface treatment methods vary according to the material, such as aluminum alloy or stainless steel. Furthermore, titanium alloys and composite materials are naturally resistant to corrosion so no surface treatment is required.
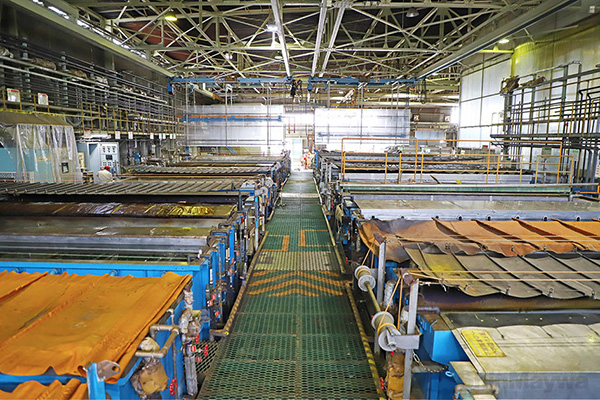
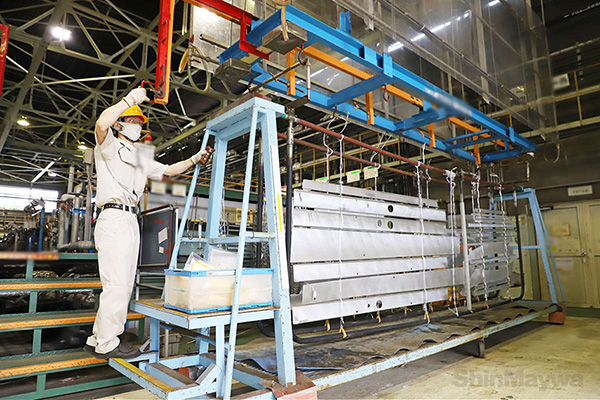
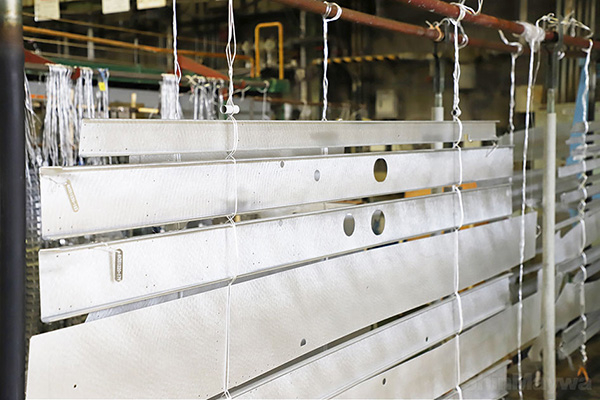
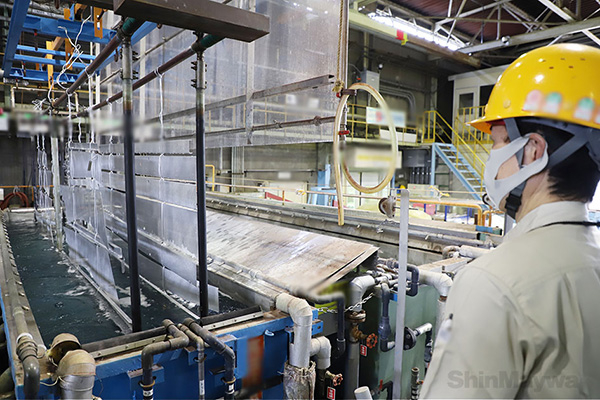
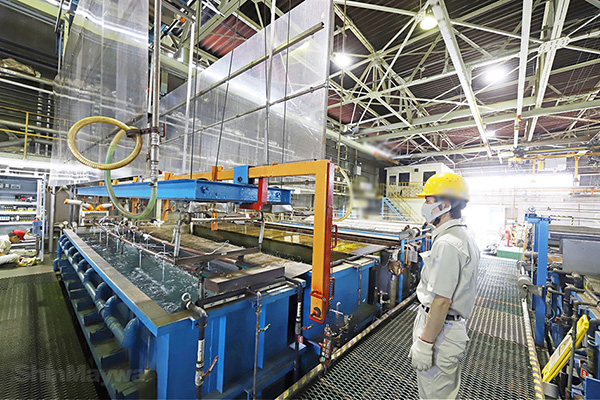
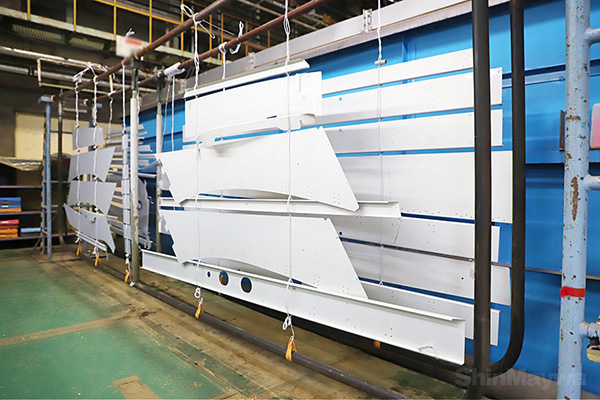
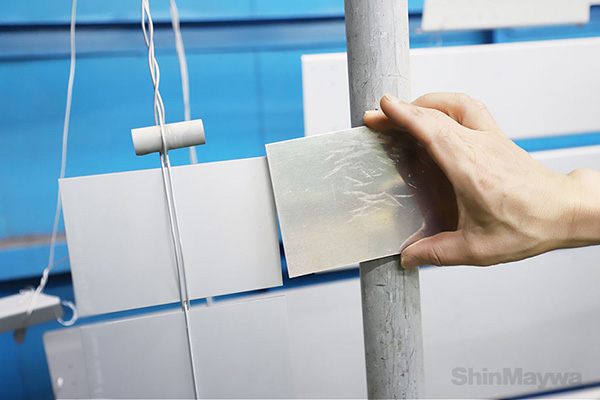
Writer Hidenori Itakura
- *This series is produced and published with the permission of the Ministry of Defense. Please do not reproduce the content and images of this series.