[Series] How the US-2 is made (2)
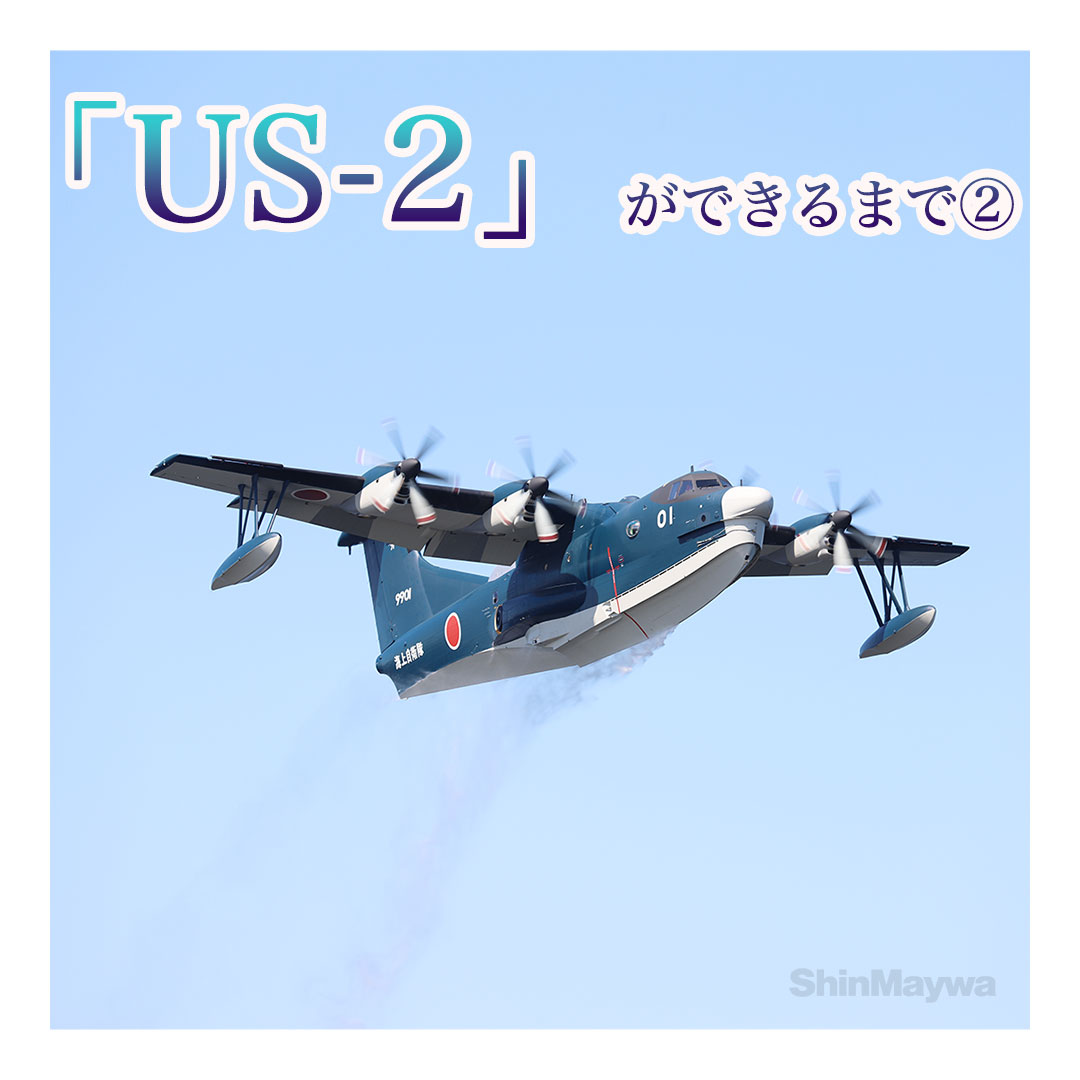
Close coverage by a professional writer
Molding of parts
—A process that combines craftsmanship and chemistry
The parts of the US-2 cut out from aluminum alloy sheets are still flat and look like development drawings. These parts are bent, drilled, and processed to create the specified shapes.
A press brake that can bend plates to any curve or angle, a hydraulic press that sandwiches a sheet between dies and applies strong pressure to form a shape in an instant, and other machine tools are used in this process. Furthermore, parts with complex shapes that cannot be machined with these machines are hammered and bent by the hands of craftsmen.
Soft and thin aluminum alloy sheets are better suited for this bending process. However, they are not strong enough for use in the US-2.
Therefore, we apply a process called “heat treatment”. Certain aluminum alloy materials have the property to harden when they are left at room temperature for a certain period of time after being heated and this property is used for parts that require strength.
Specifically, to harden the parts, an oven is used to expose the parts to high temperatures for a specified period of time. Then, they are brought back to room temperature. This expertise is a precious asset that has been passed down for about 80 years, going back to the time when ShinMaywa was manufacturing amphibians as Kawanishi Aircraft Company.
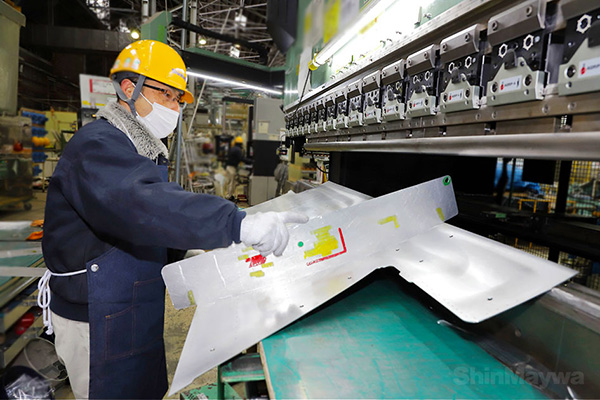
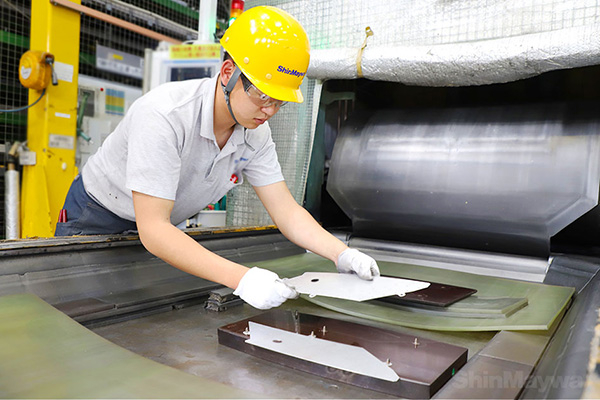
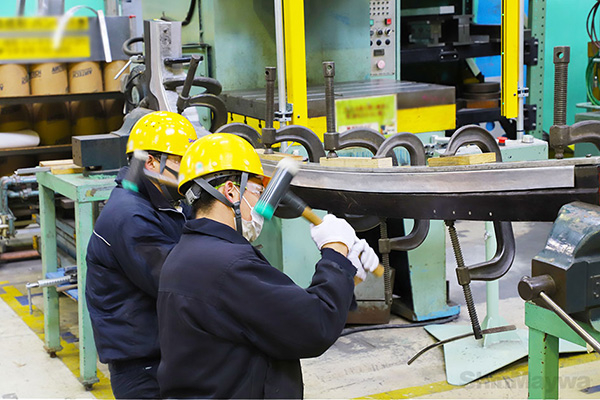
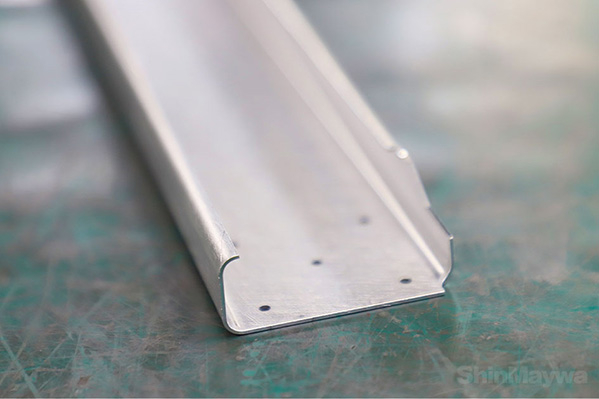
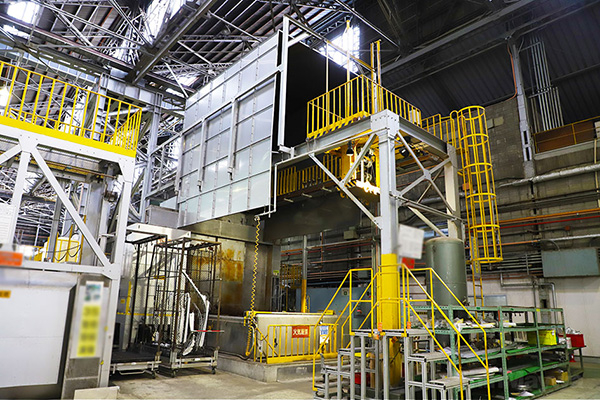
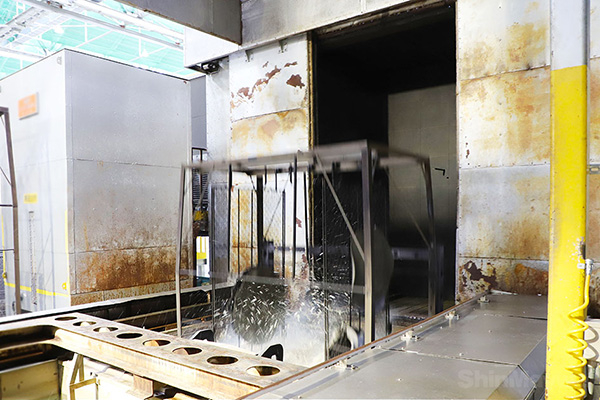
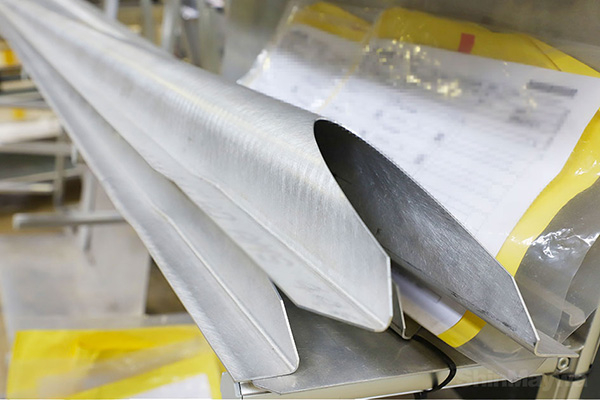
Writer Hidenori Itakura
- *This series is produced and published with the permission of the Ministry of Defense. Please do not reproduce the content and images of this series.