TR202CS
端子打機TR201Cシリーズ
新型片ハンダ端子打機TR202CS
- ハンダ槽への投入角度を最適化し、ハンダ付けの完成度を向上
- AWG28~16の中太線ハンダ加工のための新設計
- 従来同様、簡単段取りで端子圧着に早変わり
- 鉛フリーハンダに対応
簡単段取りイメージ
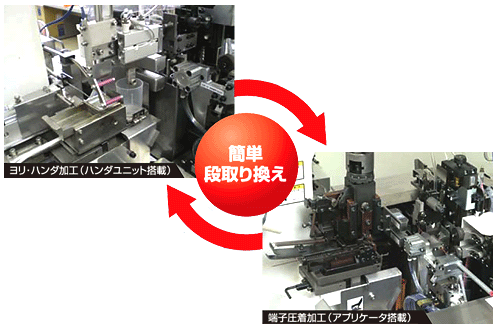
標準仕様
電源※1 | 三相AC200V ±20V 15A(50Hz/60Hz) | ||
---|---|---|---|
エア源※2 | 0.5MPa(5kgf/cm2)以上 60Nl/min以上 | ||
モータ | 9軸 ACサーボ (400W×5 クリンパ、X軸、 プレフィーダ 50W×4 カッタ、Y軸、測長) |
||
最大加工能力※3 | 両端モード:4,500本/h F側:ハンダ、R側:圧着:3,100本/h F側:ヨリ・ハンダ、R側:圧着:2,340本/h |
||
線径 | サイズ※4 | AWG16~28 | |
被覆外径 | ⌀3.2~0.8mm | ||
最大切断長 | 9.999mm(1mm単位) | ||
最小切断長※5 | 30mm | ||
切断長さばらつき(精度)※6 | ±1.2mm(1,000mm時) [±(0.00045×L+0.75)L:実測平均切断長さ] |
||
圧着能力 | 19.6kN(2t)×2基、ストローク30mm | ||
圧着端子 | オープンバレル連続端子(サイドフィード、エンドフィード) | ||
ストリップ長 | フルストリップ長※7 | F:最大30mm R:最大25mm(0.1mm単位) | |
セミストリップ長※7 | F:最大25mm R:最大15mm(0.1mm単位) | ||
ヨリ・ハンダ長さ※8 | F:2~15mm(0.1mm単位) | ||
先端ハンダ加工精度※9 | ±1.5mm | ||
使用ハンダ※10 | 糸ハンダ(ヤニなし): ⌀1.0~1.6mm | ||
ハンダ設定温度 | 400℃以下 | ||
機械寸法 | 本体(430kg) プレフィーダ(30kg) |
H1,430mm×W800mm×D920mm (本体のみ、突起部を除く) |
|
推奨使用環境温度※11 | 15~25℃ | ||
表示言語※12 | 日本語、中国語、英語(1カ国語選択) |
- ※1仕様範囲外の電圧では誤作動や機器破損の原因となります。アース線は必ず接地してください。感電や誤作動の原因となります。漏電ブレーカーを設置する場合は機械1台につき1ヶ接続してください。漏電検出電流は30mAを選定してください。
- ※2供給空気温度は0~30℃の範囲で使用できますが、空気中の水分が氷結しないことが必要です。氷結の恐れがある場合はドライヤを使用し、供給空気を乾燥させてください。空気中に、油・塵埃・カーボンなどが含まれていると空気圧式機器が正常な機能を果たさなくなります。このため、機械に供給する圧縮空気は相対湿度85%以下で、有害ガスや汚染物質(塵埃・油・カーボンなど)を多く含まぬように注意してください。これら汚染物質が多く含む恐れのある場合、各種空気清浄化機器(アフタクーラ、ミストセパレータ、ドライヤなど)をご使用ください。
- ※3切断長さ30mmの時の値です。ストリップ長さ、オーバハング長さ、その他加工条件によっては低下します。
- ※4被覆外形が大きい電線では加工ができないことがあります。
- ※5最小切断長さは、使用アプリケータ、圧着位置、オーバハング長さ、電線サイズで変化します。
- ※6使用される電線の種類によっては精度を維持できない場合があります。
- ※7入力可能値です。線径が小さくなると実加工ができない場合があります。電線サイズに応じて部品の交換、調整が必要となります。特殊な電線、端子では加工条件に制約がでる場合があります。セミストリップを行わない場合は、フルストリップは0~15mmまで使用可能です。アプリケータを取り付けた場合には、セミストリップを行う場合でもF側のフルストリップは0~25mmまで、R側のフルストリップは0~15mmまで使用可能です。
- ※8ストリップ長が短い場合に電線サイズによってはヨリの効果が十分得られない場合があります。電線サイズによってハンダ加工可能最小長さが異なります。
- ※9電線サイズによって先端ハンダ加工精度が異なります。
- ※10ハンダ供給が足りない場合はφ1.0~1.6mm内の太い径のハンダをご使用ください。
- ※11範囲外の環境温度では、電線くせ取り効果が不十分となり、ストリップ不良、圧着不良などの発生が多くなります。
- ※12表示以外の言語につきましてはご相談ください。
ハンダ加工品質の向上(当社比)
従来
ハンダ槽の上まで電線を移動させ、電線を下に向けてハンダ槽に付け込む方式(押付け方式)
新機能
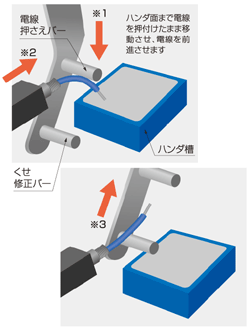
- 電線押さえバーは電線先端をハンダ液面まで下げる役割 ※1 をし、その後のハンダ付けは電線を前進させる進入方式 ※2 により、ハンダ加工品質が向上
- 1回のハンダ付けではきれいに付きにくい電線には、2度付け機能も搭載
- 押付けがきつい場合は電線に曲がり癖がつくため、ハンダ加工後に曲がり修正バーで電線を下から持ち上げ、曲がり癖を修正 ※3
- ハンダ槽は、鉛フリーハンダによるハンダ槽侵食対策として、特殊コーティングを施したタイプを採用
加工データの作成時間が1/3に短縮(当社比)
従来
20項目のデータ入力のため、加工データ作成に時間がかかる
新機能
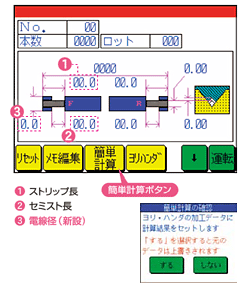
- 3つのデータ(右図中:1・2・3)を入力するだけで、ハンダ加工のノウハウを組み込んだプログラムにより、加工データを自動計算
- 誰が行っても均一なハンダ加工データ作成が可能
- 自動計算後の微調整も可能
ハンダ槽まわりのお掃除もらくらく
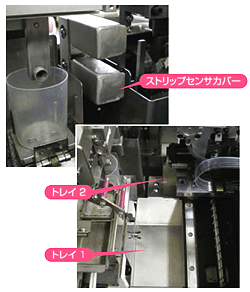
- 取り外しが簡単な脱着式トレイ/センサーカバーを新設計
- ハンダやフラックスで汚れやすい部分のメンテナンスが楽
- ステンレス製のため、フラックスの影響による錆にも強く、ハンダ、フラックス汚れの掃除も簡単
新ヨリユニットで細線~太線のヨリ加工を着実に
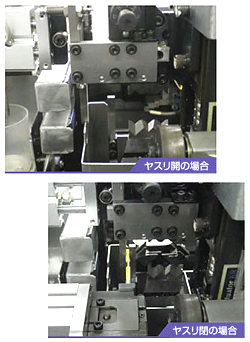
- ヤスリの電線保持力をパワーアップ。さらに、ヤスリ面を特殊加工面に改良することによりグリップ力を向上させ、AWG28~16線まで確実なヨリ加工を実現
- ヤスリを動かしながら電線を引く新設計のヨリ機構で、長いストリップ長でも根元まで均一に撚ることが可能
- ヤスリの開きを大きくしセミストリップした電線がヤスリ間に確実に進入するように改良
お問い合わせ先
製品に関するお問い合わせはこちらからお願いいたします。
ほかの製品・サービスを探す