Developed “Full Auto System (Full Auto Installation System)” aircraft passenger boarding bridge
2020年03月30日
ShinMaywa Industries, Ltd. (Head Office: Takarazuka City, Hyogo Prefecture, President and CEO: Tatsuyuki Isogawa) has successfully developed a "Full Auto System" as an option for aircraft passenger boarding bridge.
The newly developed "Full Auto System" utilizes image recognition technology using new AI (artificial intelligence), and allows the operator to press the start button once, and in addition to the automatic driving function of the conventional boarding bridge, the closure ( This system completely automates the entire process of attaching the roof (to protect from rain and wind) to the aircraft door. This system has been tested at Changi Airport (Singapore) since October 2019, and its safety and accuracy have been highly evaluated by both the airport and the airlines that use the airport.
We plan to begin accepting orders for this product in May 2020 after continuing demonstration experiments.
To date, we have commercialized an "automatic installation system" in which the boarding bridge automatically runs up to 10 centimeters in front of the aircraft, and since May 2017, it has been in operation at Tokushima Awa Odori Airport, followed by Narita International Airport. The automatic installation system currently in operation is compatible with various weather conditions and various models, including the Airbus A380, which has three doors on the aircraft, and has been highly evaluated by airport officials who have introduced it.
Comments from Tokushima Air Terminal Building Co.,Ltd.:
"Until now, installing boarding bridge depended on the skill of the individual, and the time required varied depending on the person in charge, but after introducing this system, the installation time has become constant regardless of the weather or the skill of the person in charge. As a result, the biggest benefit is that it has become easier to plan takt times.Since it can be attached reliably with a simple operation, it reduces the mental burden on personnel and eliminates human errors. This is a big step towards making the world smarter."
Currently, airports around the world are becoming smarter, and in order to further improve on-time flight rates, expectations are high for the complete automation of the process of boarding bridge to aircraft, provided that safety is guaranteed. Masu.
Under these circumstances, the newly developed "Full Auto System" further evolves the conventional automatic driving function, creating a system that does not require operator operations such as inputting aircraft model or installing the device from 10 centimeters in front. Established. Even with conventional automatic installation systems, it was possible to increase the number of compatible models by registering model information set for each aircraft, but the newly developed "Full Auto System" does not depend on aircraft model. Since the installation posture of boarding bridge on aircraft can be calculated without any need for manual work such as collecting new information or adding information to the system in order to accommodate new aircraft, there is no need for manual work. One of the features is that everything is handled automatically on the system. In addition, ``fully automatic detachment'' was also achieved by driving in the opposite direction to the attachment point.
◆Our strength: We maintain a "99.95% occupancy rate'' at Changi Airport (Singapore), where all operating boarding bridge manufactured by our company, and we have the top market share in Asia (excluding China).
Our company is a pioneer, having delivered the first domestically manufactured boarding bridge to Tokyo International Airport in 1969, and to date we have delivered more than 1,000 products to airports in more than 60 countries around the world.
In recent years, the number of applications has been increasing at airports in Southeast Asia such as Singapore and Thailand, and the company currently boasts the top share in Asia (excluding China). In particular, at Singapore's Changi Airport, a hub airport in Asia, all aircraft passenger boarding bridge currently in operation are manufactured by our company, and our group also undertakes maintenance. Our track record of meeting the airport's strict requirements of ``99.95% occupancy'' is proof of our quality, and all operating boarding bridge at Chubu Centrair International Airport, Osaka International Airport, and Kobe Airport are manufactured by our company. We have earned the trust of major airport facility companies both domestically and internationally.
In the future, we will continue to contribute to maintaining and improving high occupancy rates, which are the lifeblood of airports, by using our technological capabilities to respond to the challenges faced by airport facilities, with an eye toward expanding into other regions including Southeast Asia. Masu.
1. Aircraft passenger boarding bridge automatic installation system “Full Auto” flow
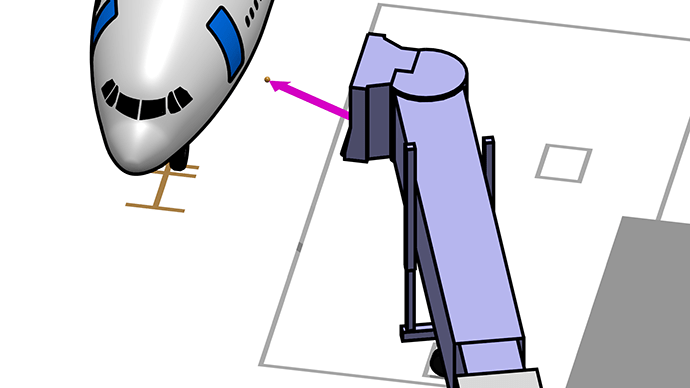
- 1 After confirming that aircraft has entered the gate, the operator presses the start button once.
- 2 Boarding bridge uses two cameras from the park position to photograph aircraft door from different angles, automatically detects the three-dimensional position of the door, and calculates boarding bridge attitude 1 meter in front of the door, which is the waypoint. .
(If the door cannot be detected, move the tip of boarding bridge called the "cab" and take a picture, then search for the door again. Even if the door is viewed diagonally, it can be detected correctly.)
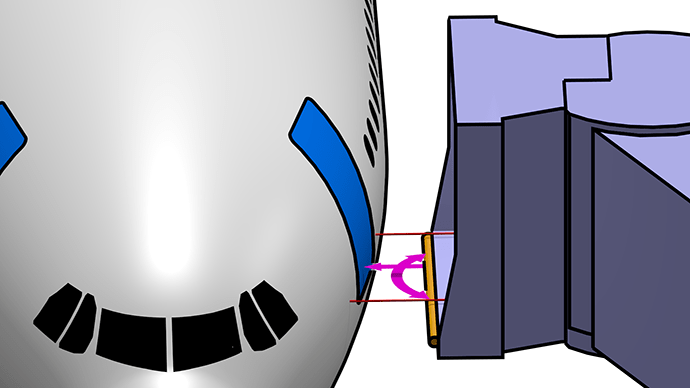
- 3 Boarding bridge will move 1 meter in front of the door and then stop.
- 4Once again, two cameras detect the door position, and at the same time, a laser rangefinder is used to measure the parallelism of the door and cab to calculate the precise mounting position.
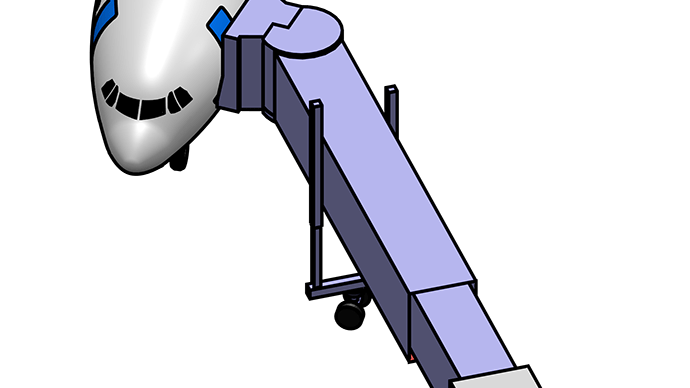
- 5While measuring the distance to aircraft with a laser rangefinder, move to the installation position and install it.
- 6The mounting sequence ends when the closure (the roof part to keep out the wind and rain) is closed and the system transitions to auto-level mode (a function that follows the height of aircraft, which fluctuates according to guest boarding and alighting). (At this point, the aircraft door can be opened and closed.)
2. Features of “Full Auto System”
- 1It is possible to run boarding bridge automatically until the installation is completed on the aircraft door.
- 2 Just press the start button once to complete the "fully automatic installation" operation. Two cameras directly detect the door, so there is no need to input the model. It has also been successful in saving labor at airport facilities, where staff shortages are an issue, and in preventing human errors.
- 3 Due to the adaptive ability of AI-based machine learning, it is more resistant to changes in weather, environment, and aircraft paint than normal image processing, and can detect doors in a wide range of situations. Even if detection fails due to special environments or painting, it is possible to retrain and update the learning model.
3. Specification
Dimensions & Performances | Conventional | Fully automatic system | |
---|---|---|---|
1 | Model identification | ・Operator selects and inputs | ・No need to input model ⇒Adopts a mounting sequence that does not depend on the model |
2 | Reached position | ・10cm in front of aircraft door ⇒Final installation is done manually by the operator |
・Installed state (State where the door can be opened: Closure (*1) closed, auto level mode (*2) ON) |
3 | Operability | ・Deadman method by operator (runs only while the operator presses the button under visual confirmation) | 1 push of start button by operator (using operation panel) |
- *1 Roof part to protect from rain and wind
- *2 A function that follows the height of aircraft, which changes as passengers get on and off.
Contact Information Regarding this Matter
About this release
ShinMaywa Industries, Ltd. Public Relations/IR Department Corporate Planning Headquarters
1-1 Shinmeiwa-cho, Takarazuka, Hyogo, 665-8550, Japan
About products
ShinMaywa Industries, Ltd. Airport Facilities Group
Global Sales Department Sales Headquarters Parking Systems Division
7-12-14 Ueno, Taito-ku, Tokyo, 110-0005, Japan
The information published in this content is current as of the date of publication.
Please note that this information may differ from the latest information due to changes in our group's business strategies and organization.