Developed automatic aircraft passenger boarding bridge installation system
July 6, 2018
ShinMaywa Industries, Ltd. (Head Office: Takarazuka City, Hyogo Prefecture, President and CEO: Isogawa Tatsuyuki) has developed an automatic installation system for aircraft passenger boarding bridge, and has received orders from Narita International Airport and Changi Airport. Delivery to both airports is planned in February 2019.
The feature of the newly developed automatic installation system is that it automatically approaches the aircraft passenger boarding bridge to within 10 centimeters of aircraft door (boarding/exit), and we are the first company in the world to put it into practical use. This system, which consists of two cameras, an image processing device, and a laser rangefinder, utilizes artificial intelligence (AI) and is different from conventional autonomous driving systems, which were limited to getting within 100 centimeters of the aircraft door. Compared to preset travel), the distance that can be automatically approached to aircraft has been significantly shortened. This eliminates the need for operator skills and allows even inexperienced users to perform highly accurate installation operations with the touch of a button. In addition to the ``labor shortage'' and ``reducing operation training time,'' which are issues facing domestic airport operations, it is expected to help improve on-time flight rates, which is one of the important issues for airport facilities.
Prior to receiving orders from Narita International Airport and Changi Airport, we have been conducting a demonstration experiment of this automatic attachment system at Tokushima Awaodori Airport since October 2015. As a result of testing over thousands of times, we were able to confirm its safety, which led to its adoption at both large international airports. Furthermore, Tokushima Awaodori Airport continues to use this system even after the demonstration experiment has ended.
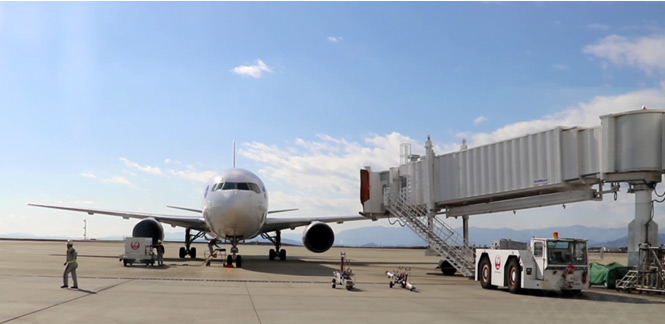
- Our strength: Maintaining "99.95% occupancy rate'' at Changi Airport (Singapore), top share in Southeast Asia
- Our company is a pioneer, having delivered the first domestically manufactured aircraft passenger boarding bridge to Tokyo International Airport in 1969, and to date we have delivered more than 1,000 products to airports in more than 60 countries around the world. In recent years, adoption has expanded in Southeast Asian countries such as Singapore and Thailand, and we currently boast the top market share in the region. In particular, at Singapore's Changi Airport, all of boarding bridge currently in operation are manufactured by our company, and we also undertake their maintenance. The quality of our work is backed by our track record of meeting the airport's strict conditions of 99.95% occupancy, and we have recently received an order for 100 units for Osaka International Airport and Kansai International Airport. We have earned the trust of airport facility companies.
In the future, we will continue to work with a view to expanding into Southeast Asia and other Asian countries where we have not yet entered, and will strive to develop products that contribute to improving airport occupancy rates by responding to the issues faced by airport facilities.
1. Automatic loading system
[Method for detecting aircraft door position using aircraft passenger boarding bridge]
- 1A door detection camera is installed inside the cab, which is the tip of aircraft passenger boarding bridge. The target position for installation is detected by photographing the aircraft door.
- 2By stopping about 1 meter before aircraft door and photographing the door again using the "door detection camera," the error from the target position is corrected.
- 3 At the same time as "②'', an "AI camera'' also installed on the outside of the "cab'' takes pictures, and using both images, an "AI image processing device'' identifies the aircraft door position, achieving high accuracy. Realizes the detection of
[Features]
- 1It is possible to automatically run aircraft passenger boarding bridge up to 10 cm in front of aircraft door.
- 2 Operation ① can be performed by simply pressing one button, so even inexperienced users can perform highly accurate installation operations without undergoing technical training.
- 3Deep learning learns from changes in weather and envrionmental, so the more you use it, the more accurate it becomes. In addition, deep learning can also be used to support the entry into service of aircraft that were not configured at the time of introduction.
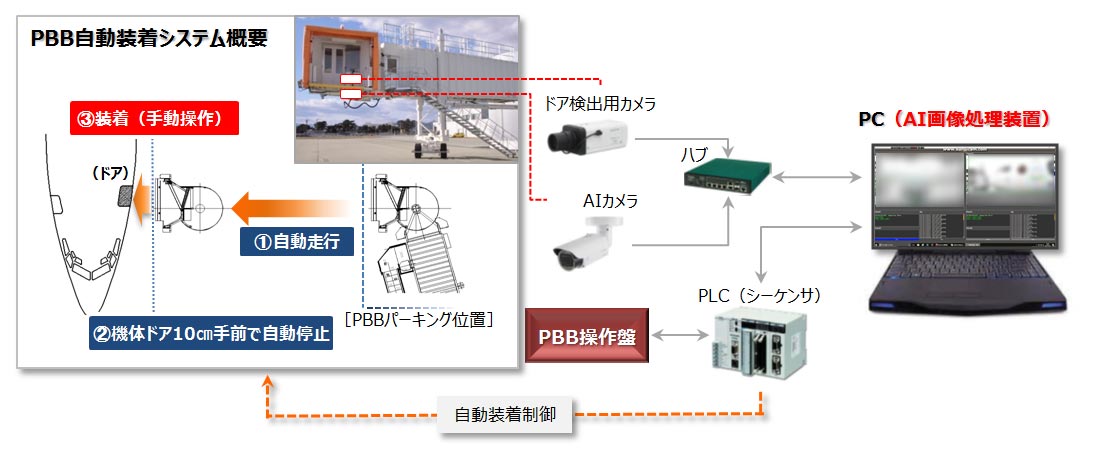
- * PBB= aircraft passenger boarding bridge
[specification]
Operation/method | Adopts a dead man system that automatically travels up to 10cm in front of aircraft door only while the button is pressed. Subsequent operations must be performed manually by the operator. |
---|---|
Security verification | As before, visual confirmation by the operator is required for safety inside the tower and on the apron and for aircraft (including engines) to avoid collisions. |
Applicable models | The target model determined at the time of ordering will be the applicable model. Separate setup is required for models other than those applicable. |
Operating environmental | If aircraft door is difficult to see or cannot be seen due to rainstorms, heavy fog, snowfall, etc., it must be operated manually. |
2. Outline of automatic attachment system demonstration experiment
Place | Tokushima Awaodori Airport |
---|---|
Cooperating organization |
|
Period | October 2015 - March 2018 |
Experimental model (type of aircraft) | B767, B737, E170, A320, A321 |
Number of automatic mounting systems installed | 3 units (installed on all aircraft passenger boarding bridge at the airport) |
Contact Information Regarding this Matter
About products
ShinMaywa Industries, Ltd.
Airport Facilities Group Sales Headquarters Parking Systems Division
5-16-5 Higashiueno, Taito-ku, Tokyo, 110-8620, Japan
For news organizations
ShinMaywa Industries, Ltd. Secretary/Public Relations Group President's Office
1-1 Shinmeiwa-cho, Takarazuka, Hyogo, 665-8550, Japan
The information published in this content is current as of the date of publication.
Please note that this information may differ from the latest information due to changes in our group's business strategies and organization.