自動車市場向け新型自動電線処理機「TRD510」を開発
2015年05月08日
新明和工業株式会社(取締役社長 大西 良弘)は、このたび、ワイヤーハーネス(組電線)に使用される電線の測長、切断、端末加工といった一連の作業を自動で行う自動電線処理機「TRD510」を開発、5月10日から販売を開始します。
「TRD510」は、自動車用ワイヤーハーネス向け電線の加工に特化した新機種で、業界最高クラスの加工能力「1時間当たり5,000本」と、自動車市場向けの当社従来機種に比べ、加工能力を11%向上するとともに、小型化により、設置占有面積も26%縮小を実現しました。
近年、欧米・中国を中心とする自動車需要拡大に伴い、自動車市場向けワイヤーハーネスの生産量も増加傾向にあります。また、自動車に搭載される機器は電動化が進み、最近では、予防安全機能に必要となるセンサーやカメラ用に、電子回路による制御機器が標準装備されるなど、自動車1台当たりのワイヤーハーネスの使用量も増加しています。
更に、主に自動車需要の拡大が著しい新興国において、自動車の価格競争が激化しており、自動車メーカーから、ワイヤーハーネスに対する低価格化への要求も厳しさを増しています。
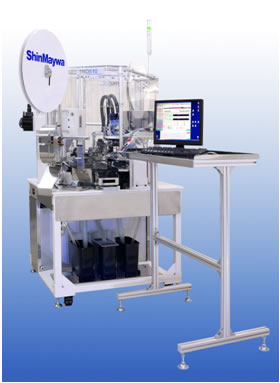
このような状況下、自動電線処理機には、高度な加工性能に加え、生産性の一層の向上が求められており、「TRD510」の開発に当たっては、これまで民生用品市場向けとして実績があり、細線対応に優れ、小型で高速・高精度化を実現している「TR500」のプラットフォーム(基本構造)を採用し、より細い電線に対応できるようになったほか、品質に対する基準が厳しい自動車市場向けに必要な機能を標準装備したことで、加工スピードを向上させながらも品質を維持し、生産性向上を実現しました。
具体的には、端子を圧着する際のさまざまな設定(圧着条件出し)を容易にする「デジタルクリンパ」を圧着機に搭載したことで、ワイヤーハーネスの生産時に重要視される「段取り替え時間※1」を短縮したほか、電線を送りながら計測する測長ユニットを、従来機の金属製ローラーによる電線送り機構から、「TR500」で実績のある「ベルトフィード機構」に変更し、電線へのダメージを軽減することで、アルミ電線を含め※2、細線化が進む最新の自動車用電線にも対応しました。加えて、同ユニットに、高速送りを可能にするフィードバック補正制御も搭載したことで、切断長の計測精度を更に向上させました。
今後も自動車の需要拡大と電動化が進むことが予測され、市場拡大が見込める中、当社では、自動電線処理機の世界的な市場でのシェア拡大を目指し、品質の向上および生産性の追求と、アフターサービスの更なる充実を図ってまいります。
- ※11台の自動電線処理機で、線種の異なる加工を行う場合の、次の電線の加工開始までの準備時間
- ※2アルミ電線は、メーカーにより電線の性質が異なるため、加工テストによる事前確認を行います。カッター、クランプ等特殊電線用の交換部品も提供可能です。
1.「TRD510」の特長
(1)最大5,000本/時の業界最高クラスの加工能力実現と省スペース化により、生産性が向上
(電線1本当たりの加工費低減に貢献)
プラットフォーム
- 高速・高精度加工で実績のある「TR500」のプラットフォームを採用
- 自動車市場向け当社従来機「TRD301」より小型化を実現し、設置占有面積を26%縮小
圧着機
- 圧着条件出しを容易にする数値制御により段取り変え時間を短縮する、2.0トンクラスのデジタルクリンパを搭載)
カッタユニット
- 高い制御機能により電線の高速・高精度切断を実現する、最新のサーボモーターを駆動機構に搭載
測長ユニット
- 「TR500」で実績のあるベルトフィード機構の採用により、電線へのダメージを軽減し、細線化が進む最新の自動車用電線に対応。同じくフィードバック補正制御も搭載することで、特に長い切断長加工時の精度が向上
標準装備
- 端子圧着判定装置(TCM)
- バッドワイヤーチョッパー(上記TCMで不良が検出された電線の端子を切り落とす装置)
(2)メンテナンス性の向上
カッタユニット
- 刃の交換が容易な機構
- フロント/リアのストリップ刃、切断刃の各6枚を独立構造にしたことにより、刃の個別交換が可能
グリスアップ箇所減(当社従来機比)
- 従来機「TRD301」の29箇所に対し、「TRD510」は17箇所と約4割削減
2.販売開始日
2015年5月10日(標準機)
2015年7月10日(シール挿入機)
3.価格
820万円(標準仕様/税別)
4.主な販売先
ワイヤーハーネスメーカー
5.販売目標
2015年度:100台
6.諸元
新型両端端子打機「TRD510」標準仕様
型 式 | TRD510 | |
---|---|---|
最大加工能力 | 両端端子圧着時 5,000本/h(切断長:100 mm)、4,200本/h(切断長:500mm) 3,750本/h(切断長:1,000mm) |
|
加工電線 | サイズ |
0.13~1.25 mm2 AWG 26~18
|
外径 | 最大 φ3.0 mm | |
切断長さ | 50 ~ 20,000 mm | |
ストリップ長さ | 1~16 mm | |
電線送り | ベルトフィード機構 実用標準速度 6 m/s、最大10 m/sまで可能 | |
圧着機 | デジタルクリンパ | |
圧着能力 | 19.6 kN | |
圧着端子 | オープンバレル連続端子(サイド・エンド) | |
標準装備 | ストリップセンサ、端子有無センサー、ジョイントセンサ、電線過負荷センサー、電線滑り検知、端子圧着判定装置(TCM)、バッドワイヤーチョッパー | |
駆動モーター | 全軸ACサーボモーター | |
消費電力 | 最大 約0.4 kWh | |
必要供給エア | 0.5 MPa 150 ℓ/min(ANR) | |
入力・操作画面 | 液晶画面、マウス、キーボード入力による操作 | |
安全装備 | 部分開閉式フルカバー | |
電源 | 三相 AC 200V ±10%以内 (50/60Hz) トランス対応 : 240V、380V、415V ±10%以内 (50/60Hz) |
|
機械寸法 | 幅1,100×高さ1,850×奥行1,810 (mm) 幅1,700×高さ2,110×奥行2,100 (mm)
|
|
本体質量 | 約690 kg | |
主なオプション | コンベア(切断長さ:2m、3m、5m用)、PC台付き電線トレイ(切断長さ2mまで対応) キャリアカッター、端子過負荷検知 |
本件に関するお問い合わせ先
製品について
〒230-0003
神奈川県横浜市鶴見区尻手3-2-43
報道機関の方
〒665-8550
兵庫県宝塚市新明和町1-1
以上
このコンテンツに掲載している内容は、発表日現在の情報です。
これらの情報は、当社グループの事業戦略および組織の変更などにより、最新の情報と異なる場合がありますのでご了承ください。