2. Mechanism of the vacuum thin film coating system
-- How is a thin film with a high degree of purity and adhesiveness produced?
To form a thin film
Generally, there are two methods of forming a thin film in the vacuum thin-film coating technology: Physical Vapor Deposition (PVD) that utilizes the physical movement of particles and Chemical Vapor Deposition (CVD) that utilizes a chemical reaction. Here, we would like to give a brief explanation of the evaporation method and the sputtering method included in PVD.
The evaporation method is the easiest way to form a thin film, where the material of the film is heated, dissolved, and evaporated in a vacuum and adheres to the object, as shown in Chart A. It can be compared to the phenomenon where steam from a bath tab condenses into water drops on the ceiling.
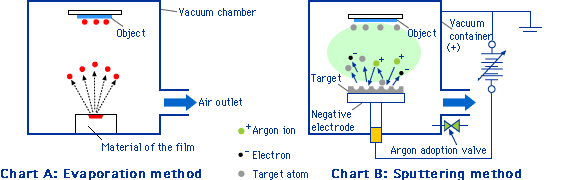
On the other hand, the sputtering method applies a voltage of some hundred volts between the vacuum chamber and an electrode (target) made of the film material, as shown in Chart B. If a small amount of inert gas (e.g., argon) is added to the chamber, electricity is discharged. The particles of the gas assume a positive charge by the energy of the electricity. The positively charged particles are pulled by the strong power of the negative electrode and they collide with the electrode. The shock flicks a part of the material and it becomes particles, which form a film on the target.
For example, the gas in an old fluorescent lamp runs into a filament (a part of an incandescent lamp that emits heat and light) and particles from the filament adhere to the inner surface of the glass tube. This is the cause of the black stain at the ends of a fluorescent lamp. This is thought to be a type of sputtering film coating.
To form a thin film of high quality
This simple method, however, cannot form a quality thin film with high degree of purity and adhesiveness. The important point is to maintain a vacuum in the chamber when forming a film.
For example, if you form a film in the atmosphere (a) or in a low vacuum (b), the particles of the film material try to move toward the object on the ceiling of the chamber but are obstructed by vapor, oxygen, nitrogen, and carbon dioxide in the air. Thus, they seldom reach the object and cannot form a film. Furthermore, even if the particles reach the object, it causes a number of problems where the adhesiveness of the film is weak or the film material bonds with other substances in the air. The solution is to maintain a high vacuum in the chamber (c) to reduce unwanted substances. This produces a quality thin film of high degree of purity and adhesiveness.
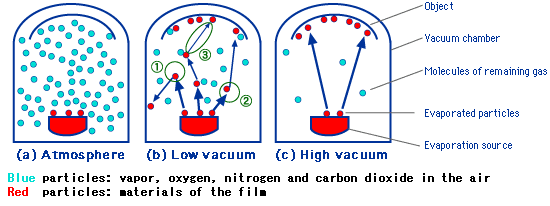
To maintain a vacuum
Based on this principle, the vacuum thin-film coating system forms a thin film in a vacuum chamber. It consists of a vacuum chamber, vacuum pumps, and valves as shown below. At the moment, we do not have such a powerful pump that can exhaust air from the level of atmosphere to high vacuum at once, so that two types of pumps are required as shown below: a roughing air displacement pump (atmospheric pressure 105 Pa to several Pa) and a substantial air displacement pump (less than several Pa).
At the beginning, only the roughing valve is open, and one rough air displacement pump works to exhaust air. Then, the rough valve is closed, and the remaining two valves are opened to activate both the roughing and substantial air displacement pumps connected in series. By doing this, the pressure inside the chamber reaches the level where a film can be formed.
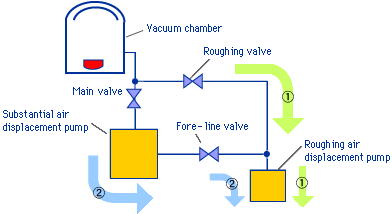
This is the mechanism of the vacuum thin film coating system.
In the next issue, we will introduce the efforts and unique technologies of ShinMaywa in the vacuum thin-film coating business.